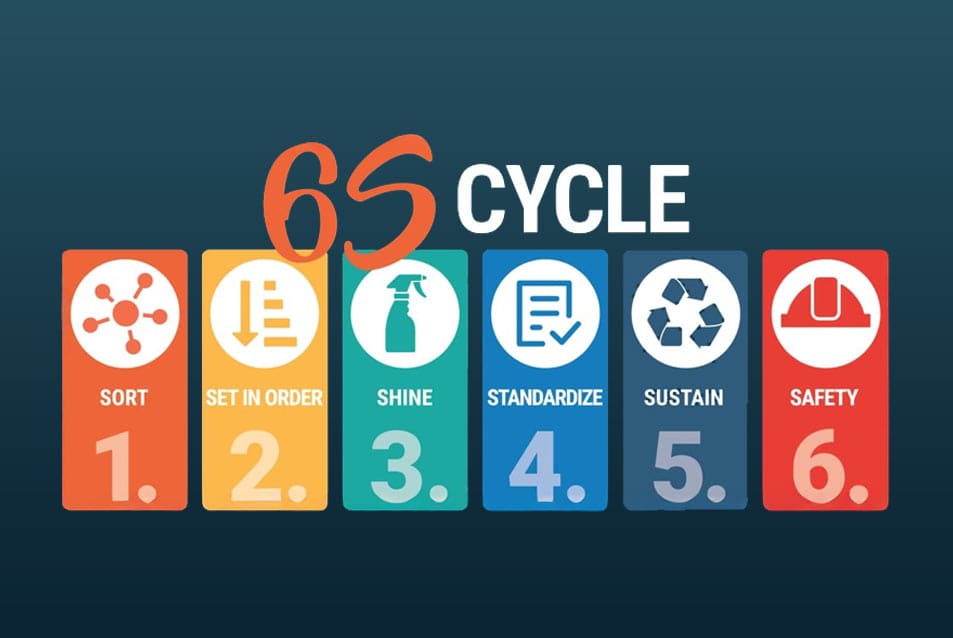
At Larson Tool, we take great pride in our commitment to efficiency, quality, and customer satisfaction. Our approach is centered around the principles of LEAN manufacturing and 6S methodology, which drive continuous improvement and operational excellence. These methodologies enable us to deliver superior products while ensuring a streamlined and cost-effective process for our customers. In this blog, we will explore how our LEAN and 6S techniques provide tangible benefits to both current and potential customers.
Understanding LEAN and 6S
What is LEAN Manufacturing?
LEAN manufacturing is a systematic approach to minimizing waste without compromising productivity. The goal is to create more value for customers by eliminating inefficiencies, reducing costs, and improving workflow. LEAN principles focus on the following:
- Identifying and eliminating waste in processes
- Optimizing workflows to increase productivity
- Improving quality through continuous evaluation and refinement
- Enhancing responsiveness to customer needs
What is 6S?
6S is an expanded version of the traditional 5S methodology, with an added focus on safety. It consists of:
- Sort – Removing unnecessary items to declutter the workspace
- Set in Order – Organizing tools and equipment for easy access
- Shine – Cleaning and maintaining work areas to prevent defects and hazards
- Standardize – Establishing uniform processes to ensure consistency
- Sustain – Creating a culture of discipline to uphold standards
- Safety – Prioritizing workplace safety to protect employees and improve efficiency
The Benefits of LEAN and 6S for Larson Tool Customers
1. Enhanced Product Quality
By integrating LEAN and 6S into our operations, we ensure that every product meets the highest quality standards. A clean, organized, and efficient workspace reduces defects and rework, resulting in products that perform reliably. Our focus on continuous improvement allows us to identify and address potential issues before they impact customers.
2. Cost Savings for Customers
Efficiency is at the core of LEAN manufacturing. By eliminating waste and optimizing resources, we reduce production costs—savings that we pass on to our customers. Whether it’s through minimized material waste, improved energy efficiency, or optimized labor utilization, our LEAN approach ensures cost-effective solutions without compromising on quality.
3. Faster Turnaround Times
A streamlined workflow means faster production cycles. Our 6S organization ensures that tools and materials are readily available, reducing downtime and increasing throughput. Customers benefit from shorter lead times, allowing them to meet tight deadlines and stay competitive in their respective industries.
4. Greater Flexibility and Customization
LEAN manufacturing allows us to be more agile in responding to customer needs. Whether it’s a custom order, a design modification, or an urgent request, our flexible approach enables us to adapt quickly. This responsiveness is particularly valuable for customers requiring tailored solutions or low-volume, high-mix production runs.
5. Improved Workplace Safety and Reliability
Safety is a critical component of the 6S methodology. A safer work environment means fewer accidents, reduced downtime, and greater employee morale—all of which contribute to more reliable and consistent production. Customers can trust that our processes are designed to ensure the safety of our workforce while delivering dependable products.
6. Stronger Supplier and Customer Relationships
At Larson Tool, we believe that operational excellence goes beyond our internal processes—it extends to our relationships with suppliers and customers. By implementing LEAN and 6S, we foster strong partnerships built on trust, efficiency, and shared goals. Customers benefit from a supplier that is committed to transparency, reliability, and continuous improvement.
Real-World Impact: LEAN and 6S in Action
One of our recent initiatives involved optimizing our stamping and metal forming processes through value stream mapping. By identifying bottlenecks and reorganizing workflows, we reduced cycle times by 20% while maintaining superior product quality. Additionally, our enhanced 6S practices led to a 30% reduction in workplace incidents, reinforcing our commitment to safety and efficiency.

Another example of LEAN and 6S in action was our redesign of the tool changeover process. By implementing quick-change tooling and standardized procedures, we decreased setup times by 40%. This efficiency allows us to respond to customer demands faster and with greater flexibility.
We also applied 6S principles to our warehouse management system, reorganizing inventory layouts and implementing digital tracking. This resulted in a 25% reduction in retrieval times and a significant decrease in misplaced materials, ultimately ensuring that customers receive their orders accurately and on time.
These improvements directly translate into better outcomes for our customers’ faster delivery, lower costs, and unparalleled quality assurance.
Conclusion: The Larson Tool Commitment
At Larson Tool, our dedication to LEAN and 6S methodologies is more than just a strategy—it’s a commitment to delivering the best possible products and services to our customers. By continuously refining our processes, eliminating waste, and prioritizing safety, we provide tangible benefits that set us apart in the industry. Whether you’re a long-time partner or a potential customer considering Larson Tool, you can trust that our approach is designed to maximize value and efficiency.
Ready to experience the Larson Tool difference? Contact us today to learn how our LEAN and 6S-driven approach can benefit your business.
About Larson Tool & Stamping Company
Since its inception in 1920 in Attleboro, MA, Larson Tool & Stamping Company has been making a difference as a valued supplier of precision metal stampings and assemblies to hundreds of companies in the United States. Larson provides high-quality, cost-effective solutions with our wide range of capabilities that include forming, stamping, deep drawing, machining, assembly, brazing, coining, and water-jetting. Through significant investment in leading-edge manufacturing equipment and the loyal support from customers and co-workers, Larson perpetuates the commitment made by our founders to do whatever is necessary to meet and exceed customer expectations.
Find out first-hand and contact us now to see for yourself.