Metal stamping is a widely-used manufacturing process that shapes metal sheets into various forms using different types of dies and presses. If you’re wondering when it’s worth building a tool for metal stamping, you’re in the right place. This guide will help you figure out the best time to invest in tooling based on low, mid, and high-volume production needs.
Understanding Metal Stamping Tools
Before we dive into production volumes, let’s quickly go over the types of tools used in metal stamping:
- Single-Operation Dies: These are for simple tasks like cutting, punching, or blanking.
- Progressive Dies: These handle multiple operations in one go as the material moves through the die.
- Transfer Dies: These are for complex parts with several steps; they transfer the part through different stations within the die.
Choosing to build a tool involves weighing the initial investment, manufacturing efficiency, part complexity, and volume requirements.
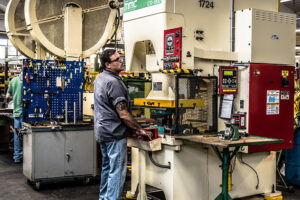
Low Volume Production
Characteristics:
- Volume: Typically, less than 10,000 parts.
- Tooling Costs: High relative to production volume.
- Production Goals: Usually prototypes, test runs, or limited runs.
Tooling Considerations:
- Cost-Benefit Analysis: For low-volume production, investing in a high-quality, durable tool might not be cost-effective. The initial investment can be hefty, and spreading this cost over a small number of parts might not make sense.
- Alternative Approaches:
- Soft Tooling: Consider using softer materials like zinc-based alloys or non-heat-treated steel. These are less expensive and suitable for short runs. While they may not last as long or be as precise as hardened steel, they’re often good enough for prototypes or low-volume needs.
- Manual or Semi-Automatic Tools: These can be cheaper and faster to produce. They’re ideal for low volume runs where precision and repeatability aren’t as critical.
- 3D Printing and Rapid Prototyping: Sometimes, 3D printing can create complex dies for prototypes or very low-volume production. It’s not always suitable for high-precision or high-stress applications, but it can be a cost-effective way to test your product’s design.
- Tooling Design: For low volumes, simplify the tool design to reduce costs. Focus on meeting the part’s specific needs while keeping the design straightforward.
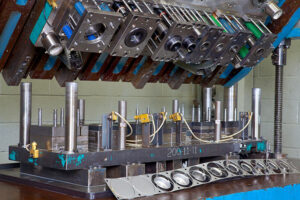
Mid Volume Production
Characteristics:
- Volume: Between 10,000 and 100,000 parts.
- Tooling Costs: Significant but spread over more parts.
- Production Goals: Often for moderate-sized runs, test phases, or market launches.
Tooling Considerations:
- Cost Efficiency: At this volume, a more durable and precise tool becomes more justifiable. The cost per part goes down, making the initial investment more reasonable.
- Tooling Material:
- Steel Tools: For mid-volume production, hardened steel tools are a good choice. They’re more durable and precise than softer materials and can handle higher production rates. The cost is offset by longer tool life and better part quality.
- Tooling Complexity:
- Progressive and Transfer Dies: Investing in more complex dies, like progressive or transfer dies, can be beneficial. They allow for multiple operations in a single pass, boosting efficiency and accuracy.
- Maintenance: Regular maintenance is crucial to keep the tool working well throughout its lifecycle. Your tooling needs to be robust enough to handle wear and tear while consistently producing high-quality parts.
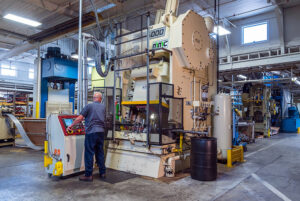
High Volume Production
Characteristics:
- Volume: More than 100,000 parts.
- Tooling Costs: High, but the cost per part is low due to large production numbers.
- Production Goals: Large-scale manufacturing, cost-efficiency, and high precision.
Tooling Considerations:
- Investment Justification: The high initial cost of tooling is easily justified by the low cost per part due to the large volume. The focus here is on maximizing production efficiency and maintaining consistent quality over a long run.
- Tooling Material:
- Hardened Steel Tools: For high-volume production, you need hardened steel tools. They offer the best durability, precision, and longevity, crucial for maintaining high production rates and part consistency.
- Tooling Complexity:
- Advanced Dies: Investing in advanced dies with multiple stations or complex operations is often necessary. These help achieve high throughput and accuracy. Progressive dies and transfer dies are common for handling the complexity and volume efficiently.
- Production Efficiency:
- Automation: High-volume production often involves automated stamping processes to boost efficiency further. Automation reduces labor costs and increases consistency in part production.
- Maintenance and Quality Control: Continuous maintenance and rigorous quality control are essential. Regular inspections and maintenance routines help avoid production downtimes and ensure the parts consistently meet specifications.
Summary and Decision-Making
When deciding whether to build a tool for metal stamping, consider the following factors:
- Volume of Production:
- For low volumes, alternative methods or soft tooling might be more cost-effective.
- For mid-volume production, investing in more durable tooling can provide better efficiency and part quality.
- For high volumes, advanced, durable tooling is essential for maximizing production efficiency and maintaining consistent quality.
- Cost Considerations: Evaluate the cost of tooling relative to the volume and compare it to alternative manufacturing methods.
- Part Complexity: Complex parts might justify the investment in advanced tooling, particularly at mid to high volumes.
- Production Goals: Consider your production goals—whether it’s a prototype, limited run, or large-scale production—and choose the tooling accordingly.
By assessing these factors, you can make a well-informed decision about building a tool for your metal stamping project, ensuring that the process aligns with your production needs and budget targets.
About Larson Tool & Stamping Company
Since its inception in 1920 in Attleboro, MA, Larson Tool & Stamping Company has been making a difference as a valued supplier of precision metal stampings and assemblies to hundreds of companies in the United States. Larson provides high-quality, cost-effective solutions with our wide range of capabilities that include forming, stamping, deep drawing, machining, assembly, brazing, coining, and water-jetting. Through significant investment in leading-edge manufacturing equipment and the loyal support from customers and co-workers, Larson perpetuates the commitment made by our founders to do whatever is necessary to meet and exceed customer expectations.
What all this translates to is that—whether your next project requires progressive die stamping, deep drawing, in-die assembly, precision machining, or value-added operations—Larson is well-equipped to do the job.
Find out first-hand and contact us now to see for yourself: [email protected]